PolyMod® Advantage
PolyMod®: Low-Friction, High-Performance Sealing
Seal friction can negatively affect system performance, efficiency, and life. PolyMod® high performance thermoset and thermoplastic rubber materials are polymer modified to have very low coefficients of friction and optimized wear life giving them significant advantages over conventional elastomer seal materials.
Breakout Friction Values PolyMod® High Performance Materials vs. Standard Materials
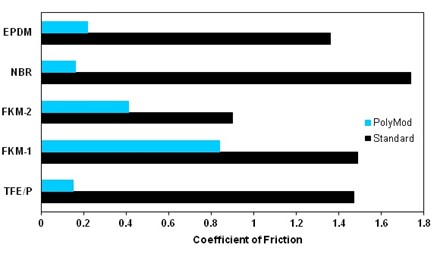
Running Friction Values PolyMod® High Performance Materials vs. Standard Materials
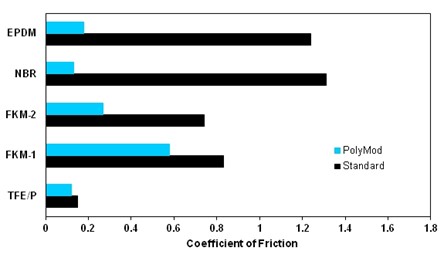
Reduced Abrasive Wear
Even in hydraulic systems, seal materials are worn and abraded. PolyMod® materials significantly show improvement in wear life over conventional elastomer.
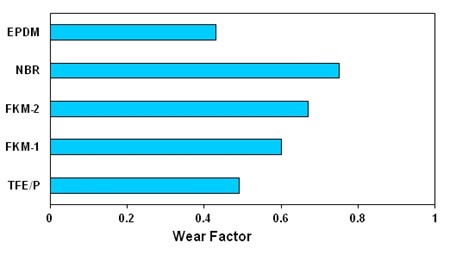
Graph Notes
- Evaluations using Taber Abrasion (ASTM D3389)
- H-18 wheels at 1 kg loading
- Values are the mean of the three separate runs taken
- The wear of the PolyMod® materials is shown as a factor less than 1.0, indicating improved wear resistance when compared to the standard materials
No Adverse Material Property Changes
PolyMod® does not change physical properties. The PolyMod® process can be performed on O-rings to custom shapes and from seals to other rubber parts.
AS568-214 NBR O-Rings - Original Physical Properties
Physical Property | Standard NBR Material | PolyMod® High Performance Material |
---|---|---|
Tensile Strength (psi) | 2230 | 2158 |
Elongation (%) | 290 | 287 |
100% Modulus | 551 | 556 |
Hardness (Shore A) | 71 | 71 |
TR10 (°F) | -24 | -27 |
AS568-214 NBR O-Rings - Physical Properties After Aging
70 hours @ 302°F in ASTM #3 Oil
Physical Property | Standard NBR Material | PolyMod® High Performance Material |
---|---|---|
Tensile Strength Change (%) | -52 | -37 |
Elongation Change (%) | -38 | -28 |
Hardness Change (pts.) | 7 | 7 |
Volume Swell (%) | 16 | 16 |